Silicates Application
Textiles
Applicable Products:
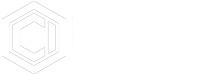
Sodium silicates are used for many applications in textile mills, including:
Sodium silicates are supplied as solution in water at different weight ratios of Si0 to NaO. Depending upon their ratio, the liquid sodium silicates provide a wide range of chemical and physical properties.
Bleaching
The decomposition of peroxide solution is accelerated by the catalytic action of some common metals such as copper, iron and manganese. The effect of iron on the decomposition of peroxide liquors increases with greater alkalinity. Stabilization with sodium silicate reduce the amount of hydrogen, peroxide consumed per pound of goods bleached, thus lowering the bleaching cost.
Continuous Bleaching
In J-Box operations, the cloth- after being put through the caustic saturator-passes into a steam tube. Then the material enters the J-Box where the caustic acts on the cellulosic material. Silicate is introduced in both the caustic saturator operation and in the peroxide saturator sequence.
In another system, steam tubes are not used prior to the goods entering the J-Box, but instead steam is introduced at the bottom of each I-Box. After leaving the first “J” the goods are washed and squeezed. A saturating bath of peroxide and silicate follows. Finally, the cloth travels from the second “J” to the washer, the squeezer and then to the white room.
Successful continuous bleaching is often conducted at a 1:1 ratio of silicate to 50% hydrogen peroxide. However, some mills have increased the ratio to 2:1 silicate-to- H0, for heavier weight fabrics. Since plant equipment, materials, and individual requirements differ, the user can best determine the amount of silicate for each application prior to fullscale use.
Silicate build up is preventable by regular rinsing of process equipment. Most build up is removed with warm water. Excessive build up may require use of hot water and/or a dilute solution of caustic soda. Normal precautions should be observed when working with caustic soda solutions.
In another system, steam tubes are not used prior to the goods entering the J-Box, but instead steam is introduced at the bottom of each I-Box. After leaving the first “J” the goods are washed and squeezed. A saturating bath of peroxide and silicate follows. Finally, the cloth travels from the second “J” to the washer, the squeezer and then to the white room.
Successful continuous bleaching is often conducted at a 1:1 ratio of silicate to 50% hydrogen peroxide. However, some mills have increased the ratio to 2:1 silicate-to- H0, for heavier weight fabrics. Since plant equipment, materials, and individual requirements differ, the user can best determine the amount of silicate for each application prior to fullscale use.
Silicate build up is preventable by regular rinsing of process equipment. Most build up is removed with warm water. Excessive build up may require use of hot water and/or a dilute solution of caustic soda. Normal precautions should be observed when working with caustic soda solutions.
Pad-Batch Dyeing
Pad-batch dyeing is a textile dyeing process which offers simplicity, versatility and flexibility without major capital investment in equipment. It can increase production and improve dying quality and reproducibility, while reducing processing costs. Both knitted and woven goods containing cellulosic fiber can take advantage of this process.
Sodium silicates are utilized as part of the fixation alkali, providing the necessary buffering to keep reactive dyes stable. Selection of the proper sodium silicate is crucial for optimal dye yield and performance. When knitted greige goods are pad-batch dyed, the silicate helps to sequester knitting oils and saponi spinning waxes.
Sodium silicates are utilized as part of the fixation alkali, providing the necessary buffering to keep reactive dyes stable. Selection of the proper sodium silicate is crucial for optimal dye yield and performance. When knitted greige goods are pad-batch dyed, the silicate helps to sequester knitting oils and saponi spinning waxes.
Detergency Operations
Cloth becomes stained with oils, grease, and dirt as it travels from one operation to another. Such soil must be removed. Temporary sizing must also be removed.
The combination of highactive alkali and soluble silica is responsible for the ability of silicates to provide the following six important detergency functions;
The combination of highactive alkali and soluble silica is responsible for the ability of silicates to provide the following six important detergency functions;
- Wetting the soil particles
- Neutralizing fatty acid soils
- Saponification of triglycerides and greases
- Deflocculating clay and dir
- Suspending soil
- Preventing soil redeposition.
Despite sudden loads of acidic soil, silicate holds the cleaning solution at a sustained pH level. Because of this buffering action, intial supplies last longer in the detergent bath. Detergent solutions without buffered alkalis are soon exhausted by acid soil, by resulting in a sharp-off of pH and consequent loss of cleaning action.
Corrosion Inhibition
Corrosion in water lines, metal tanks, vats, and humidifying systems of textiles mills is effectively and inexpensively controlled through the introduction of liquid sodium silicates. Active metal such as copper, brass and aluminum are particularly vulnerable to corrosion in the absence of silicate’s protection. Treatment is particularly valuable in naturally soft or zeolite-softened water which ordinarily attacks metal rapidly.